Tungsten carbide and ceramic knives
Our tungsten carbide and ceramic knives are specially manufactured according to customer requirements. Information on technical data is not possible for this reason.
Highly wear-resistant cutting tools from DIENES
Taking into account the current level of automation of the machines and the correspondingly high investment costs, the key to success lies in reducing downtimes. In addition to the necessary design improvements in the knife holders and knife mountings, the use of highly wear-resistant materials for the knife edges aims at achieving a considerably longer knife service life. This was achieved after many years of development with inserted tungsten carbide of the brand “CONTRODUR” and furthermore with corresponding cutting rings of the brand “DISIMET” help to reach these targets.
In order to be able to decide on a suitable material, the user should clarify the specific application with the knife manufacturer. The following procedure has proven successful at the DIENES plants for tungsten carbide and ceramic knives:
- Checking the cutting material specification
- Optimisation of the upper blade material and geometry
- Optimisation of the bottom knife material and geometry
- Implementation of the material advantage through peripherals (for example precision knife holder)
- Exact definition of knife shear angles and cutting force
Ceramic knife from DIENES-DISIMET
DIENES achieves the longest service life with circular bottom knives in rewinders and sheeters that are equipped with cutting edges made of technical ceramics. Depending on the material to be cut and the operating conditions, ceramic knives achieve 10 to 20 times the service life of conventional steel knives. Compared to tungsten carbide tipped blades, the service life is further improved by a factor of 2-3. In the production of technical ceramics, various processes can be used which have an effect on service life and prices.
Tungsten carbide knives from DIENES-CONTRODUR
The use of tungsten carbide tipped bottom knives is also suitable for improving tool life, as they cut reliably and without chipping even with difficult materials. If the use of tungsten carbide tipped bottom knives is compared under the same conditions with regular bottom knives made of “normal” tool steel, the tungsten carbide tipped bottom knives with a selected grain size last approx. 8-10 longer than bottom knives made of standard tool steels.
Use of the tungsten carbide and ceramic knives
The goal is longer tool life. Depending on the application, various material concepts are available to solve your cutting problems with tungsten carbide or ceramic-tipped cutting edges. Highest quality and precision are required to achieve cutting success.
Both cutting materials are chemically inert and exhibit the highest wear resistance. Of utmost importance are the reproducible and precisely defined operating conditions. Knives and knife holders may only have the slightest concentricity deviation and side impacts. Improper handling will lead to immediate break-out of the sensitive and hard knife edges.
The use of tungsten carbide and ceramic knives in fully automatic slitting systems guarantees reproducible and precisely defined operating conditions and makes full use of the service life. The use of the DIENES Easy Set adjustment aid has also proven its worth.
Your advantages
- Harder than steel
- Chemically inert
- optimised grain size
- extreme edge retention
Safety catch groove for tungsten carbide and ceramic knives
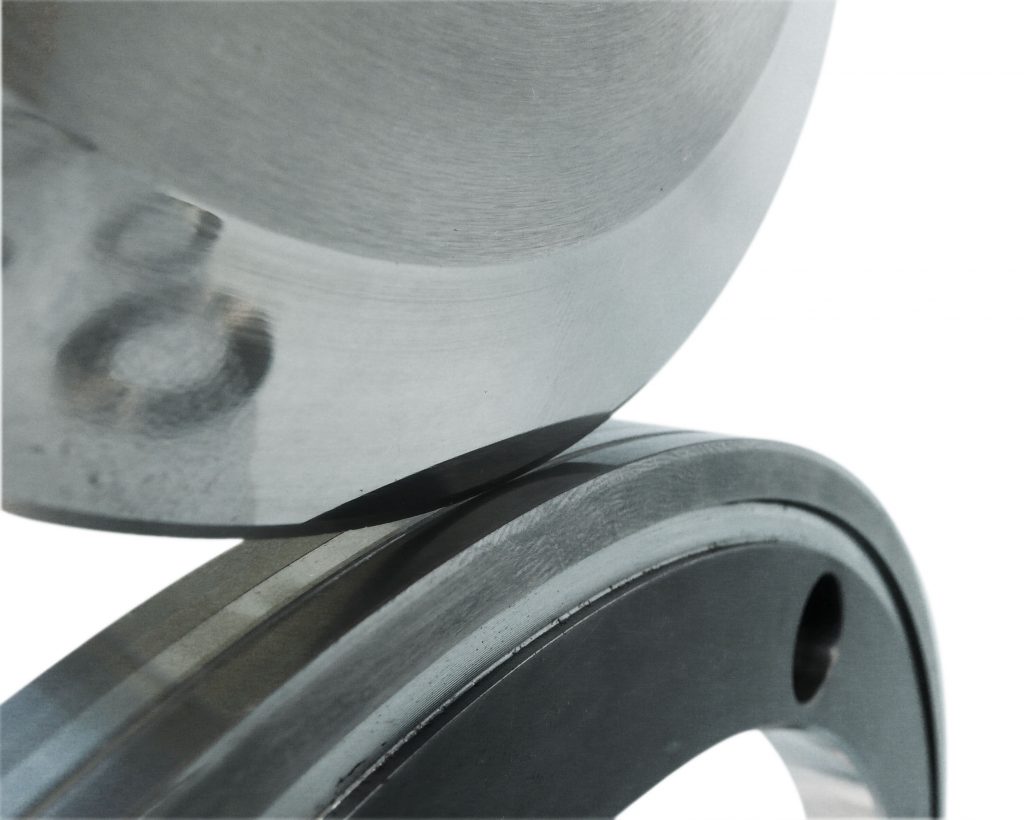
With competition knife holders, it can happen that the knife edge of the upper knife separates, loosens or damages the carbide ring from the knife carrier of the lower knife due to incorrect positioning, malfunctions or an incorrect stroke sequence. Another danger is that, due to the high cutting speed, particles detach from both top and bottom knives. This poses a high risk of injury to the operating personnel.
To reduce these dangers, DIENES has developed bottom knives with safety catch grooves. The bottom knife is provided with a circumferential groove for fixing the top knife. When the top knife runs onto the outer diameter of the bottom knife, the top knife is caught in this groove. This prevents the knife from penetrating the transition between the carbide ring and backing material.